BIRLA CARBON BLOG
INSIDER KNOWLEDGE FOR ALL THINGS CARBON BLACK
Circularity Profoundly Affects the Auto Industry – Choice of Black Pigment
Reading Time: 4.5 minutes
Circularity and the Auto Industry
The auto industry has integrated sustainability into its strategy and manufacturing processes for many years. However, it is recognized that the implementation of sustainability is still fragmented and lacking on several . Especially troublesome is the lack of initiatives for carbon efficiency and resource management throughout the value chain. The adoption of circular economy principles is expected to mend these.
The circular economy is among the top three initiatives in terms of impact on sustainability, along with recycling of waste and end-of-life disposal. Automotive companies and regulators are planning far reaching initiatives to align with the circular economy. For example:
- The European Commission is “considering rules on mandatory recycled content” for certain plastic components of new vehicles,
- Ford Motor Company intends to achieve carbon neutrality globally by 2050, while setting interim targets to more urgently address climate change challenges,
- Volvo Car Corporation has ambitions to be a circular business with circular products by 2040. And to generate annual CO2 savings of 2.5 million tonnes and 100 MUSD of cost savings by 2025 through adoption of circular economic principles.
The main sustainability elements that are practiced by the auto industry are listed in Table 1. In this blog we concentrate on the materials purchased through the supply chain since efforts placed here could lead to faster and inexpensive improvements in sustainability.
Table 1 Sustainability Efforts Across the Automotive Value Chain
Organization | Initiative |
---|---|
R&D and engineering |
|
Manufacturing and operations |
|
Vehicle usage |
|
Marketing and sales |
|
Supply chain |
|
Table 1 Sustainability Efforts Across the Automotive Value Chain
R&D and engineering |
|
Manufacturing and operations |
|
Vehicle usage |
|
Marketing and sales |
|
Supply chain |
|
Circular Auto Materials
The circular materials workstream is focused on the pressing need to decarbonize materials, instituting closed-loop recycling processes and using renewable energy sources. The materials of concern should include the manufactured parts raw materials, additives, and processes that go into manufacturing such parts. Creating a total package where most or all of the ingredients are at least sustainable or fully circular is where the overall largest impact on sustainability will be achieved.
New generations of sustainable materials in the auto industry are made from environmentally efficient materials. Newer materials will consist of advanced plastic and composites parts to replace metal. Many of these materials will use carbon black as a color enhancing , and in many applications, carbon black provides increased durability and performance – two essential elements to sustainability.
Continua™ Sustainable Carbonaceous Material (SCM) – A More Sustainable Additive
Continua™ 8000 SCM is a new product considered to be a sustainable alternative to carbon black for the auto industry, i.e. a sustainable carbonaceous material (SCM). Continua™ 8000 SCM, a recovered material from end-of-life tires, offers a significant and quantifiable reduction in carbon footprint and increased circularity.
When assessing the environmental impact of automotive products, researchers require a full life cycle assessment (LCA) to allow a comprehensive evaluation. Scoring environmental impact based solely on recyclability, biobased content, or recycled content can be misleading. One must dig deeper for a comprehensive picture of environmental costs including raw material production and energy conservation.
A life cycle assessment of Continua™ SCM compared to conventional furnace carbon black demonstrates that when supplied at full capacity, over 220,000 tonnes of direct and indirect CO2 emissions will be eliminated on an annual basis.
Improved Sustainability in Black Pigmented Plastic Parts
Vehicles today are comprised of approximately 50% plastics by volume and 15-20% by weight. Plastic parts have historically come with a heavy environmental load including high GHG emission, pollution, and depletion of petroleum resources. These issues are expected to be mitigated with new technology, albeit at an investment in time and cost. The exchange of a carbon intensive additive with one that is carbon negative will provide improved circularity with marginal cost increase.
Carbon black is the most widely used black pigment for thermoset or thermoplastic products. Continua™ 8000 SCM can aid both the plastics and automotive industry by providing the following sustainable features and benefits.
- Quantifiable CO2 savings to meet customer targets
- Consistent quality, performance, and color response
- Fully GADSL compliant for use in automotive applications
- Good dispersion and surface finish
- Pelletized for easy storage and conveying
- Lower melt flow allows faster processing or high concentration in masterbatches
The procurement departments can take on a strategic role to influence sustainability for incoming products by specifying circular black pigment in plastic auto parts. They are ideally placed to manage the planning and coordination that crosses organization lines. To succeed, there must be complete transparency of the chemical composition for materials and their environmental implications. One must look at the complete environmental picture. A circular economy is not just about recycling or using biobased materials, it requires a fundamental shift in how materials are sourced and produced.
Birla Carbon Can Help
Continua™ SCM embodies Birla Carbon’s untiring determination to innovate and create sustainable business solutions for different industries. Various supply options and in-depth technical knowledge are available to minimize the cost of introduction.
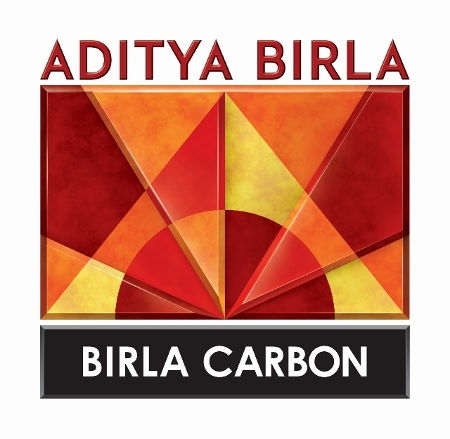
Dr. Kerstin Schrinner is the Global Sector Head for Plastics at Birla Carbon. In this function she is responsible for the sectors strategy to shape the future of our company while maximizing our current value proposition to customers and markets. Kerstin brings over 20 years of global experience in marketing functions in the plastic industry.
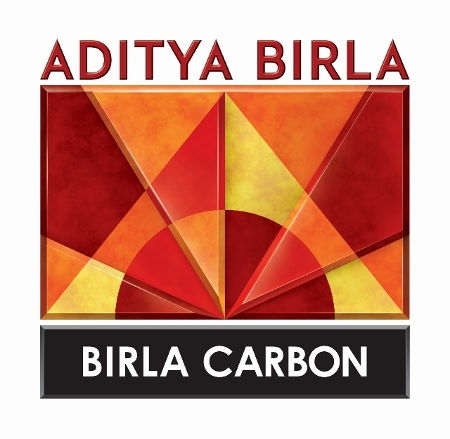
Dr. Gilles Moninot is Business Head, Continua™ at Birla Carbon. In this function, Gilles is responsible for the development, industrialization, and commercialization of the Continua™ product line destined to increase circularity in the rubber, plastic, and coating industries. This new line of Continua™ Sustainable Carbonaceous Material is a testimonial to Birla Carbon’s declared ambition to achieve Net Zero Carbon Emissions by 2050. Gilles brings over 25 years of global experience in R&D, Product Safety, and Sustainability in the carbon black industry.
WANT TO LEARN MORE ABOUT CARBON BLACK AND THE PROPERTIES THAT MAKE IT IDEAL FOR YOUR PLASTICS, COATINGS, AND INKS APPLICATIONS?
Leave A Comment