BIRLA CARBON BLOG
INSIDER KNOWLEDGE FOR ALL THINGS CARBON BLACK
Extracting Value from Carbon Black to Meet High Jetness Demands – Part 2
Reading Time: 5.5 minutes
Introduction
In Part 1 of this blog series relating to carbon black and high jetness demands, we focused on extracting the value via optimizing compounding aspects, including process design, equipment, and formulation selections to maximize the dispersion. For this follow-up article, the design of carbon black for high jetness applications will be presented. This will include important features of carbon black and the benefits delivered. We will demonstrate how carbon black products can be engineered to deliver a specific balance of performance and dispersibility to satisfy formulator compounding constraints as well as end-user color requirements. Birla Carbon’s Raven portfolio of products will be presented for this high jetness application.
Birla Carbon High-Jetness Carbon Black Products
As discussed previously, surface area and structure are two fundamental parameters that define a carbon black product and determine its application performance. Specifically, external surface area, or statistical total surface area (STSA), is the primary performance predictor of color, and it is closely correlated to the mean particle size. The finer the particle size, the higher the external surface area. The oil adsorption number (OAN) is a measure of the three-dimensional carbon black structure or degree of aggregation. Higher structure eases the dispersibility, and thus contributes to the color performance.
Birla Carbon offers a family of Raven specialty carbon blacks designed specifically for high-jetness applications in engineering plastics, as illustrated in Table 1 and Figure 1. These products have been engineered for the best balance of performance and dispersibility for use across diverse end-use industries, including automotive, electronics, and household appliances. The distinctive morphologies of these products allow for either direct compounding or through the employment of highly loaded masterbatch materials followed by letdown to deliver a range of color response depending on the end customer needs.
Figure 1 further illustrates the balance of color performance and dispersibility as determined by the surface area and structure respectively.
Figure 1: Birla Carbon’s high jetness carbon black for plastics
Performance Attributes – Coloring, Surface Finish, and Other Properties
Coloring
Carbon black delivers a wide range of color responses for plastic applications depending on the surface area of carbon black used. Figure 2 illustrates the jetness (a) and blue tone (b) as a function of surface area. As expected, finer carbon blacks offer deeper jetness and bluer undertone. These relationships are common to a variety of resin systems, including SAN, PP, PC, PA, ABS and PP. The preferred carbon black surface area can be chosen to fit the application demands of jetness and dispersibility. The shaded area shows the high jetness and blue tonal performance of high color black and piano blacks. It is worth noting the undertone becomes bluer with the surface area, however, when the particles become much finer, the blue tone tends to decrease due to increased forward light scattering with much finer particles and elevated difficulty for dispersion.
Figure 2: Higher surface area carbon blacks deliver jetter color and bluer undertone
(Shaded area shows color performance of high color and piano blacks)
Surface Finish
Surface finish with high gloss or smoothness exhibits appealing deep jetness and blue tone. It is closely related to dispersion, physical cleanliness and processibility. Sufficiently dispersed carbon black provides a smooth surface finish which helps enhance the jet-black appearance of plastic products. Using carbon blacks such as Birla Carbon’s Ultra products with high cleanliness helps to prevent surface imperfections caused by inclusions. Typically, 1% carbon black loading or less is adequate to demonstrate the desired color appearance. This level of loading is not expected to significantly impact the processibility for extrusion or injection molding of the plastic compound. Therefore, the host resin and other components used in the compound should be the determining factors for processibility.
Other Functional Properties
Besides imparting a black color, carbon black can enhance other performance factors of a product. One of the most important properties of carbon black is its capability to absorb UV light and convert it to heat, making plastics more UV durable.
Therefore, carbon black can be used to protect products from environmental stresses such as degradation from ultraviolet radiation, enhance their weatherability and extend the outdoor service life.
Birla Carbon’s high color blacks highlighted in this article offer excellent UV durability for plastic products while delivering high jetness and blue tone performance given that adequate dispersion is achieved. However, if the application is primarily for UV protection, while these high color blacks could be used, weathering performance can be delivered with a lower surface area or medium color carbon black products. Birla Carbon has alternative carbon black solutions engineered to offer the optimum UV performance with balanced dispersibility and manufacturing cost.
Conclusions
This article discusses Birla Carbon’s portfolio of products for high jetness applications. and the balance necessary between (1) carbon black morphology (particle and aggregate size), (2) easy dispersibility and letdown via compounding process, and (3) color performance in plastic applications. The successful application of carbon black starts by defining the needs for the application and the processing capabilities that are available at hand. To ensure a successful end product, the carbon black supplier and end user must engage in informative dialog and collaboration.
Birla Carbon provides a series of high-jetness carbon black pigments within our Raven family of products that are specifically designed for use in high value plastics. These products have surface areas and a range of structure levels that allow the formulator to adjust jetness and dispersibility for specific applications. The very high jetness and surface finish properties delivered make Birla Carbon’s high color products suitable for the most demanding electronics, automotive, and consumer appliance applications. Birla Carbon has a dedicated technical team who is ready to work with our customers to discover the right carbon black solution to any application need that the customer may have.
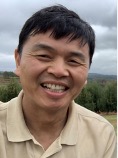
Dr. Jun Tian, PhD
Dr. Tian serves as Principal Scientist to lead a technology team and collaborate with our customers to develop carbon solutions to a variety of challenges for plastics applications. He joined Birla Carbon in 2013 and managed the plastics application laboratory to support the business growth. He holds a PhD degree in Chemical Engineering from the University of Connecticut.
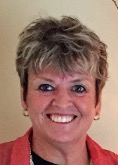
Dr. Natalie K. Harris
Dr. Natalie K. Harris began her career with Birla Carbon in 1990 at the European R&D Center in Bristol, UK, with responsibilities for the Materials Analysis Group. Dr. Harris relocated to the USA in 1998 with the role of Director, Applications Technology laboratory at the Corporate Headquarters in Marietta, Georgia, with the responsibility for managing programs for carbon black evaluations in tire, MRG, plastics, inks, and coatings. A few years later, Dr. Harris moved out of the laboratory environment to lead a global role in developing new products for the inks and coatings markets. Dr. Harris’s current role is Technical Business Development Manager, North America, for the plastics and MRG markets.
WANT TO LEARN MORE ABOUT CARBON BLACK AND THE PROPERTIES THAT MAKE IT IDEAL FOR YOUR PLASTICS, COATINGS, AND INKS APPLICATIONS?
Leave A Comment