BIRLA CARBON BLOG
INSIDER KNOWLEDGE FOR ALL THINGS CARBON BLACK
Sustainable Carbonaceous Material (SCM) is not Carbon Black
Reading Time: 2.5 minutes
Introduction
With the increased focus on sustainability throughout the value chain, recycling of end-of-life components has become increasingly important.
One product with particular attention is end-of-life tires (ELT), as these robust products are seen to be difficult to recycle. Recent advances in pyrolysis technology have allowed the development of valuable secondary raw materials from ELT supporting the circular economy.
One of the outputs from tire pyrolysis, Sustainable Carbonaceous Material (SCM), can be used as a sustainable alternative to carbon black in many applications where virgin carbon black is traditionally used. Conventionally seen as only suitable for low-value applications, these improvements now allow the use of SCM in a wider range of higher-value applications.
What is Sustainable Carbonaceous Material
Although commonly called recovered Carbon Black[1] (rCB), Birla Carbon’s research shows that you do not recover carbon black from the pyrolysis of end-of-life rubber products despite a similar appearance under a microscope (Figure 1). Birla Carbon calls this new material Sustainable Carbonaceous Material (SCM).
For Carbon Blacks there are known, fixed, relationships between colloidal properties (surface area and structure) and in-rubber properties. For example, compound viscosity, hardness, and tensile modulus all increase with increasing void volume. In Figures 2 and 3, SCMs milled to different agglomerate sizes as well as the starting char (the raw material from the pyrolysis reactor, see ‘raw rCB’ in ASTM D8178) are compared to three virgin carbon black grades. These figures show that the Mooney viscosity is higher than expected for a given structure (as measured by dynamic void volume, ASTM D7854), but the 300% modulus is lower.
The composition of SCM is also very different from carbon black. While carbon blacks are typically 99% carbon, SCM, on the other hand, contains both the various grades of carbon black in the tire feedstock and all the inorganic materials. These materials include silica (tread compounds), zinc sulphide (cure system), clays (inner liner), and other additives. These materials are integral within the SCM agglomerates and cannot be easily removed without increasing cost and environmental footprint, as well as generating waste products. This would, at least in part, reduce the environmental benefits of recycling the tires.
Conclusion
Through the pyrolysis of end-of-life tires, valuable secondary raw materials can be created. One such material, SCM, can be used as a sustainable alternative to virgin carbon black. Although commonly known as recovered carbon black, Birla Carbon has found that this material has unique chemical and performance attributes compared to carbon black and has resulted in it being given unique EC and CAS numbers.
[1] ASTM D8178
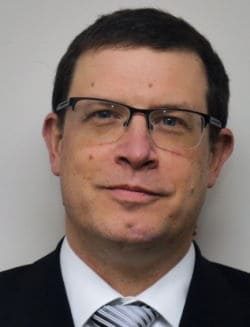
Dr. Joseph Hallett
Dr Hallett has worked in the rubber industry for over 25 years in a number of roles including product design and development, laboratory management, quality, and customer support. He re-joined Birla Carbon in 2019 and in total has worked in the carbon black industry for over 18 years. His current role is the Technical Lead for Birla Carbon’s circular product, Continua™ SCM and was part of the introduction team during the products development. Dr Hallett has a Bachelors Degree in Engineering and his PhD looked at the effect of load case on the performance of rubber compounds.
WANT TO LEARN MORE ABOUT CARBON BLACK AND THE PROPERTIES THAT MAKE IT IDEAL FOR YOUR PLASTICS, COATINGS, AND INKS APPLICATIONS?
Leave A Comment