BIRLA CARBON BLOG
INSIDER KNOWLEDGE FOR ALL THINGS CARBON BLACK
Publication Gravure Ink Performance and the Role of Carbon Black
06 / 01 / 2021 by Kirsten Barth
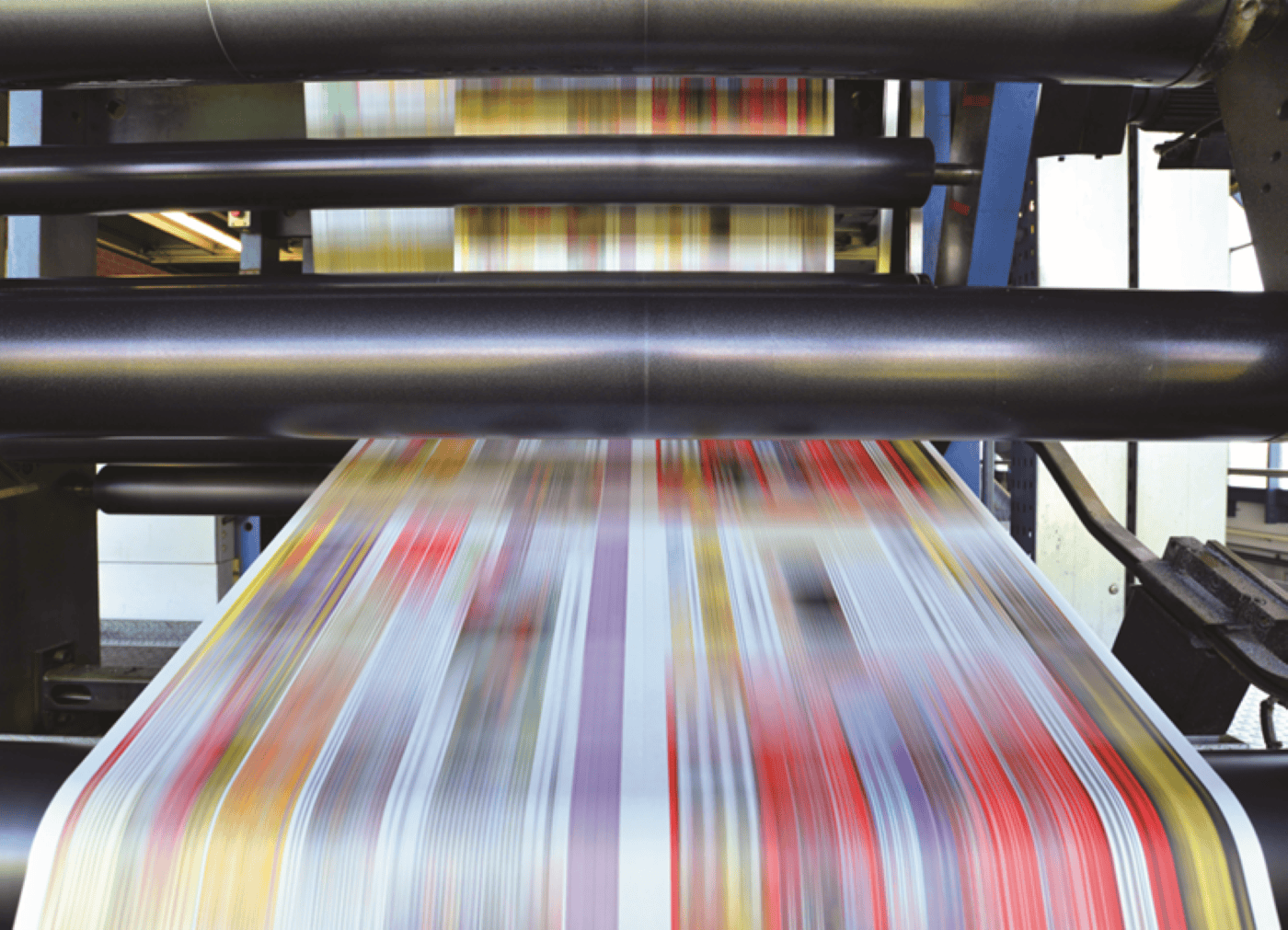
Reading Time: 3.25 minutes
What is Publication Gravure?
Publication gravure is the main application to produce print media like journals and magazines with a print volume of >300,000 copies. This high speed printing process is an automated, very efficient standard process in which the print series are printed at speeds of 13-15 m / sec., using a CYMK colour system added to the substrate by a doctor blade gravure printing process.
Coated and uncoated papers with different base weight are typical substrates for publishing gravure printing. The ISO 12647-2 standard describes the exact definition of these substrates.
A publication gravure printing ink is a low viscosity solvent-based ink, usually based on toluene. A guiding formulation comprises pigment 8-15%; resin 15-20%, additives of 0.5-5% and toluene. Hydrocarbon resins, maleate resins, cellulose, colophony or asphalt (Gilsonite) are used as binders for black ink.
What are the Performance Requirements for a Gravure Ink?
It is critical that a gravure ink has low abrasion characteristics to ensure a longer chrome cylinder lifetime. The sensitive webs between the printing dots or the chrome layer in non-gravure areas can be damaged when particles settle in the gap between the doctor blade and printing cylinder. The abrasion behaviour is impacted by very small and hard particles such as silica, coal coke, or metal. The Burda abrasion tester ATII, developed by the company Schroeder Prueftechnik, is able to simulate the conditions of the printing process and is commonly used to prove the abrasion behaviour of printing inks. The ranking of abrasion behaviour is based on weight loss and surface scratches of the chrome test plate.
Other key performance parameters for publication gravure inks are good printability (no dusting), good ink absorption/ penetration without strike through and high rub off resistance. Additional needs include low ink build up behaviour, good colour stability and high colour density. All of this must be considered while also taking into account the cost sensitive nature of this application.
How does Carbon Black Impact Ink Performance?
Carbon blacks are frequently used in publication gravure inks and a specific product needs to be selected to meet the desired performance needs. Balancing the properties of a carbon black will deliver the required colour density, jetness, gloss and rheology.
The carbon black portfolio of Birla Carbon has a range of products to meet different jetness and tonal needs. By varying the surface area, the colour response can move from low jetness to higher jetness in appearance. In addition to the final print quality, the ink formula and performance in terms of pigment loading, dispersibility and rheology will also be impacted by the surface area of the carbon black pigment.
Ink formulations printed on a porous substrate and using a high structured carbon black pigment will penetrate less into the substrate and remain on the surface. This effect can increase optical density compared to an ink formulation containing a low structure carbon black which would penetrate the substrate. The potential trade off in this situation is inferior rub off with the high structure carbon black ink. For coated, less porous substrates, the ink formulation with low structure carbon black will give the higher optical density.
The importance of low ink abrasion was highlighted already. Carbon black can affect this performance requirement, so it is important to select a carbon black pigment with few impurities.
How Can Birla Carbon Help You with Your Publication Gravure Ink Needs?
For a full understanding of the final requirements and key parameters of your ink, we would appreciate the opportunity to have an in-depth technical discussion with you. Based on a detailed knowledge exchange about both the final application and the carbon black attributes, the optimum formulation that can fully deliver the desired ink performance will be reachable. Please do not hesitate to contact our technical team for further information.
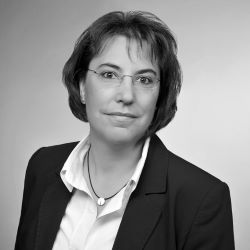
Kirsten Barth
Kirsten Barth joined Birla Carbon in 2017 as Technical Service Manager for Liquid Systems and Niche applications in Europe, Middle East and Africa region (EMEA). Kirsten is responsible for technical support of carbon black pigments and pigment preparation for inks, coatings and sealants applications.
With over nine years of technical knowledge and experience in the carbon black industry, Kirsten supports customers to find the best possible solutions for them, drives new opportunities of carbon black pigments for the inks industry and develop customer relationships on a technical level. Kirsten’s knowledge of printing inks especially liquid ink system for packaging inks, and the special paper development for packaging, digital and inkjet paper and décor paper enables her to bring new and creative solutions for customers.
WANT TO LEARN MORE ABOUT CARBON BLACK AND THE PROPERTIES THAT MAKE IT IDEAL FOR YOUR PLASTICS, COATINGS, AND INKS APPLICATIONS?
Leave A Comment