BIRLA CARBON BLOG
INSIDER KNOWLEDGE FOR ALL THINGS CARBON BLACK
Carbon Black Prolongs the Life of Plastic Pipe
Reading Time: 4.25 minutes
The Challenge: Sustainability in Water Supply
Access to safe water is the most basic human need for health and well-being. Demand for water is rising owing to local water shortages, rapid population growth, and increasing water needs from the agriculture, industry, and energy sectors. Carbon black containing plastic piping systems are a sustainable and environmentally acceptable response to this crisis that will serve generations to come.
Strong, durable, lightweight, and flexible plastic piping systems require significantly less energy to fabricate, transport, and install than metal or concrete alternatives.
Specific carbon blacks provide plastic pipes with long service life when compounded with the appropriate plastic (generally high-density polyethylene HDPE).
The requirements for pipe for potable water differ depending on geography. North America does not specify a carbon black particle size for HDPE pressure pipe or other specific material properties, and historically, Raven 520 (Table 1) type carbon blacks are used. For EU regulations (Rest of World), there are specific requirements for carbon black and high purity materials (often defined as “P-types”) are designed to meet the performance needs which are the focus of this blog.
Raven P-type carbon blacks (Table 1) provide high performance and meet all major EU regulations for critical pipe applications such as pressure piping, irrigation systems, and mining.
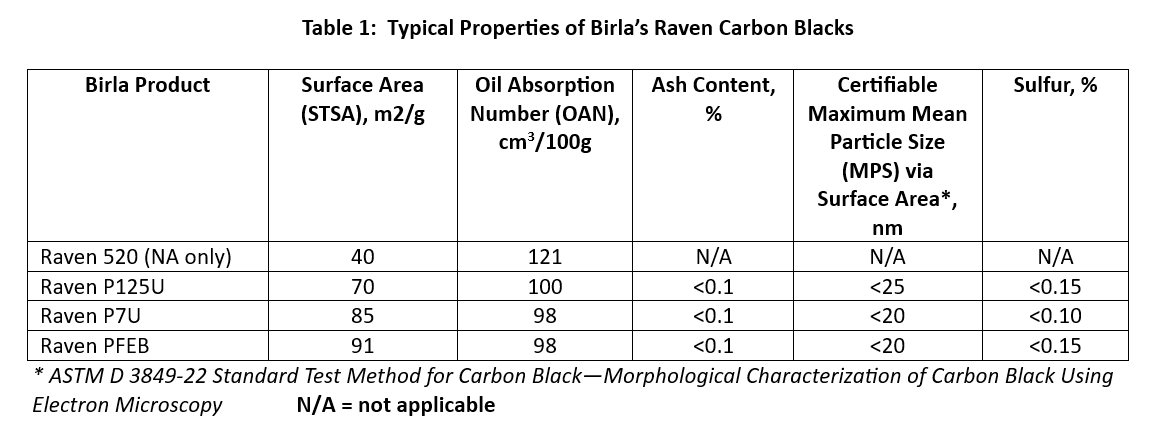
Carbon Black Particle Size, Content and UV Weathering
The typical benchmark for buried HDPE life expectancy is 50 to 100 years. However, HDPE pipes are transported and stored in an open atmosphere for a considerable length of time before installation, and many pipes are installed above the ground and exposed to sunlight. On prolonged exposure to sunlight, UV rays break the molecular chains of HDPE and drastically reduce pipe lifetime through loss of flexibility and toughness.
Carbon black is the best and most economical UV stabilizer and allows HDPE pipe to meet its optimum life expectancy. Carbon black absorbs UV radiation and thus prevents the plastic resin degradation.
The efficiency of UV absorption depends on certain properties of the carbon black. Smaller primary particles present a proportionately larger surface area to absorb UV. ISO and European standards for HDPE water pipes specify that the carbon black shall have an average (primary) particle size of less than 25 nm. Therefore, Raven P-type carbon blacks especially provide excellent UV protection. The appropriate loading level depends on the HDPE product thickness, exposure conditions, and type of carbon black. Loading to impart optimum UV protection varies between 2% and 2.5%.
Dispersion and Dispersibility
Adequate dispersibility is one of the most important parameters for carbon black in pressure pipes.
Excellent pipe quality (weathering, mechanical, surface finish) necessitates optimum carbon black dispersion. If not dispersed, then regardless of the carbon black, essential performance levels will not be met.
Raven P-type carbon blacks have a carefully crafted morphology with a good balance of the surface area and structure making it easy to disperse and adapt for fast extrusion. Good dispersion maximizes the available carbon black surface area for UV absorption and offers smooth surface finish.
Compound Moisture Absorption
Both the surface area and inorganic impurities (ash content) of a carbon black play a role in potential moisture pickup of the pipe compound. Higher surface area carbon blacks have a greater potential for moisture pickup. Moisture-related issues include voids, pinholes in the pipe wall, or rough pipe surfaces. Raven P-type carbon blacks have a unique morphological design and extremely low levels of inorganic salts. A carbon black with this balance of properties offers very low moisture absorption.
Chemical Cleanliness of Carbon Black
Chemical impurities in a carbon black used to make pipes, e.g., sulfur, toluene extract, and ash, affect organoleptic properties such as taste and odor and even the safety of the drinking water transported. These impurities need to be strictly controlled to be below certain levels required in the application regions. As shown in Table 1, Raven products exhibit excellent chemical cleanliness, and are well adopted by the industry to make water pipes
Conclusion
Water transport has become a critical global problem seeking a solution. Birla Carbon P-type carbon black in HDPE pipes provides enhanced durability and a sustainable alternative to other pipe products. The requirements for North America and Europe are different. Raven 520 type carbon blacks are used in the PPI/HSB standards for North America. For Europe, Raven P-type products meet the performance requirements for UV weathering, chemical cleanliness, and retention of mechanical properties.
For further information on Birla Carbon products for pressure pipes, reach out to the authors of this blog.
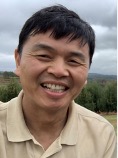
Dr. Jun Tian, PhD
Dr. Tian serves as Principal Scientist to lead a technology team and collaborate with our customers to develop carbon solutions to a variety of challenges for plastics applications. He joined Birla Carbon in 2013 and managed the plastics application laboratory to support the business growth. He holds a PhD degree in Chemical Engineering from the University of Connecticut.
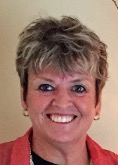
Dr. Natalie K. Harris
Dr. Natalie K. Harris began her career with Birla Carbon in 1990 at the European R&D Center in Bristol, UK, with responsibilities for the Materials Analysis Group. Dr. Harris relocated to the USA in 1998 with the role of Director, Applications Technology laboratory at the Corporate Headquarters in Marietta, Georgia, with the responsibility for managing programs for carbon black evaluations in tire, MRG, plastics, inks, and coatings. A few years later, Dr. Harris moved out of the laboratory environment to lead a global role in developing new products for the inks and coatings markets. Dr. Harris’s current role is Technical Business Development Manager, North America, for the plastics and MRG markets.
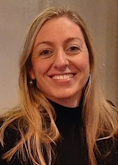
Maura Carrera
Maura Carrera has a Master’s degree in Chemical Engineering from Politecnico in Turin (Italy). After different experiences as Project Engineer for EPC companies, she started her journey in the carbon black industry passing through innovation department, production and currently working as technical referent for customers in the EMEA region, for Plastic and MRG sectors.
WANT TO LEARN MORE ABOUT CARBON BLACK AND THE PROPERTIES THAT MAKE IT IDEAL FOR YOUR PLASTICS, COATINGS, AND INKS APPLICATIONS?
Leave A Comment