BIRLA CARBON BLOG
INSIDER KNOWLEDGE FOR ALL THINGS CARBON BLACK
Ensure Your Compound Comes Out Right: Seven Common Mistakes to Avoid
9 / 20 / 2018 by Jun Tian, PhD & Dr. Ranjan Kamat
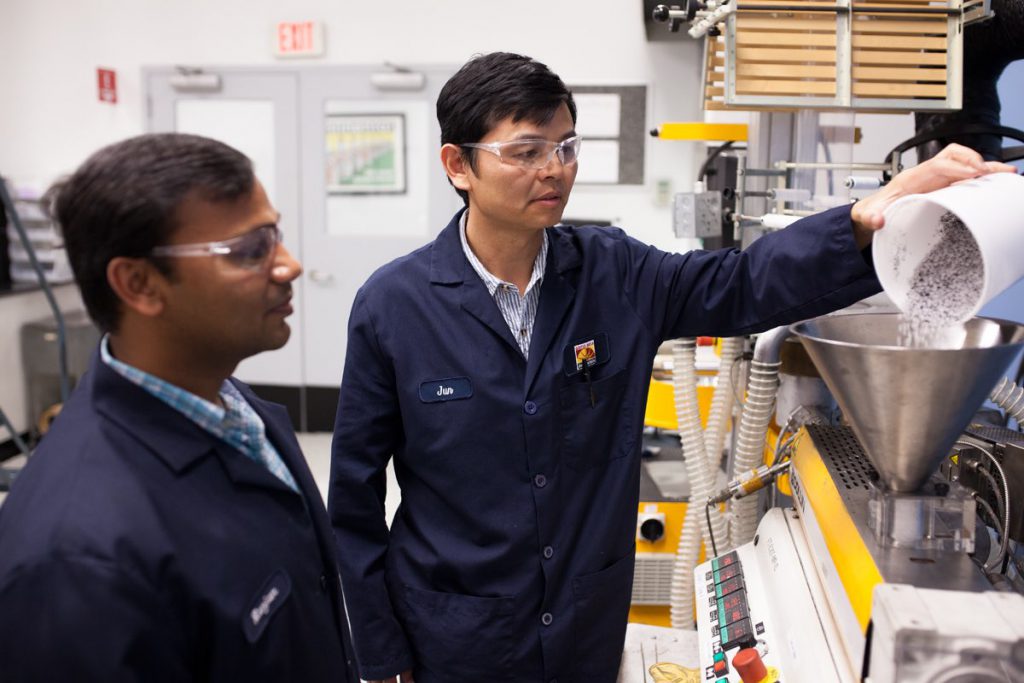
Reading Time: 3.25 minutes
Not all carbon blacks are created equal. That means you’ll need to tailor your compounding process, let-down ratio (LDR), drop-in, and other factors around the properties of the particular carbon black you’re using. Here are seven common mistakes when mixing carbon black for a plastics application — along with useful tips on how to avoid them.
Mistake 1: Choosing the wrong carbon black for the job
Since each type of carbon black is designed for a different range of applications, the carbon black you choose may have a particle size, aggregate size or surface chemistry that’s not suited for your process or application. For example, carbon black that has a high structure is most suitable for conductive applications, while one with high surface area may be better suited for applications that require high jetness or tinting. Before you buy a carbon black for your project, make sure it’s designed for your application.
Mistake 2: Using an incorrect let-down ratio
If your masterbatch’s LDR is too high or low for your intended application, you may end up with inhomogenous mixing, due to a large viscosity mismatch. By the same token, directly using carbon black in an injection molding process, without calculating the correct LDR, will lead to poor quality in your finished parts. So be sure to calculate your LDR carefully.
Mistake 3: Using an aggressive compounding process
Ideally, your compounding process should separate your carbon black agglomerates into aggregates, which get dispersed evenly among the base polymer, creating a smooth overall compound without breaking the carbon black’s structure. But I’ve seen engineers compound in machinery with the wrong screw geometry, or use a compounding process that’s far too aggressive for an electrically conductive plastic like carbon black. An overly aggressive compounding process will actually compromise your carbon black’s performance by breaking down its structure — so be sure to optimize your compounding line up-front.
Mistake 4: Handling and storing samples improperly
Even before you’ve created an optimal carbon black compound, improper handling and storage of samples can ruin all your hard work. I’ve seen samples stored in humid conditions that led to excessive moisture pick-up, or in dusty environments that gave the compound a high fine. Factors like these can negatively impact the compounding process, and thus decrease the performance of the final product. Keep a close eye on your storage environments, so this won’t happen to your carbon black.
Mistake 5: Using a familiar drop-in instead of a tailored process
Once you’ve found a drop-in process that works for one type of carbon black, you might assume it’s safe to use the same drop-in for other types. But this is a big mistake. Every drop-in process may need to be tailored to the specific carbon black product you’re using — or vice versa — to make sure your carbon black achieves its optimum performance.
Mistake 6: Failing to control impurities
Even seemingly minor impurities can negatively impact your carbon black’s performance, in terms of dispersion, conductivity and surface smoothness. Even worse, impurities can lead to higher rejection rates if you don’t control them very tightly. My suggestion is to use Ultra® carbon black products, which have excellent cleanliness.
Mistake 7: Overlooking bead hardness
I’ve often seen engineers — even experienced ones — overlook the bead hardness of their carbon black. But it’s crucial to carefully control your bead hardness to prevent problems with dispersion and performance issues with the final product. If you pay attention to bead hardness, you’ll find that your handling, as well as your dispersion of carbon black during the compounding process, will be much easier.
By avoiding these common mistakes, you’ll achieve the results you’re aiming for, while ensuring that your final product performs according to spec. With a little attention to detail, your carbon black compound can turn out exactly the way you want.
Jun Tian, PhD
Jun currently manages the plastics application laboratory and leads a team to support new product and process development and customer services. Jun has been working in the plastics industry since 2004. He especially enjoys opportunities to develop unique solutions to address customers’ specific problems. With growing laboratory capabilities, the whole team is well-equipped and eager to tackle new challenges and support the Specialty Blacks business.
Dr. Ranjan Kamat
Dr. Ranjan Kamat is the Applications Manager for the plastics segment of Birla Carbon. He received Ph.D. in Polymer Science from the University of Connecticut, USA, and Masters in Polymer Science and Technology from IIT Delhi, India. Dr. Kamat has published seven research papers in international journals and presented his work in more than ten international conferences. He has received several awards for his research in the field of polymer science and engineering.
WANT TO LEARN MORE ABOUT CARBON BLACK AND THE PROPERTIES THAT MAKE IT IDEAL FOR YOUR PLASTICS, COATINGS, AND INKS APPLICATIONS?
Leave A Comment