BIRLA CARBON BLOG
INSIDER KNOWLEDGE FOR ALL THINGS CARBON BLACK
Extracting Value from Carbon Black to Meet High Jetness Demands – Part 1
Reading Time: 5.5 minutes
Introduction
High surface area carbon blacks offer a deep black color, an appealing blue tone, and excellent surface finish. As a result, this class of carbon blacks has been gaining popularity for high value plastics applications, including automotive interior and exterior (surfaces or components, etc.), household appliances, and consumer electronics (Figure 1).
Carbon black is a widely used black pigment for thermoplastic products and can be used to create the deepest jet-black color. A carbon black engineered with a small particle size brings excellent color strength and cost-effectiveness in various finished goods.
But…. extracting the full color value of a carbon black is not always straightforward and becomes more challenging when working with finer or higher surface area carbon blacks for demanding high jetness applications.
For Part 1 of this blog, we will focus on the importance of dispersion (processing and formulation) in delivering the color value of a fine or high surface area carbon black.
A Review of Terminology
It is important to understand carbon black terminology (Figure 2).
The primary workable unit of carbon black pigment is the aggregate, which is made up of fused primary particles. The shape and degree of branching of the aggregates is referred to as structure. When packaged, carbon black exists in agglomerated form.
What do we mean by Dispersion?
To achieve the best color performance and other necessary attributes (e.g., surface finish, UV protection, gloss), it is essential that the carbon black is highly dispersed, forming a micro-dispersion, in the desired matrix. A well-dispersed carbon black will be fully de-agglomerated and uniformly distributed throughout the matrix (Figure 3).
A high degree of agglomeration (left image, Figure 3) means that the carbon black aggregates are not fully separated, and that full-color potential has not been realized. Moving from left to right, we see an increase in the aggregate population (as individual entities). This supplies the improved micro-dispersion necessary for full color development (jetness and blue tone).
Particle size dominates color development, whilst structure is a secondary factor. High jetness applications demand a small particle size or high surface area carbon black. Intrinsically, high surface area carbon blacks are harder to disperse than medium to lower surface area materials.
For this reason, understanding the challenges of dispersing/processing is essential to maximizing color performance. This will be discussed in the next few sections.
Compounding Considerations
Dispersion of carbon blacks in plastics is usually conducted by exposing the carbon black to a high shear environment such that full deagglomeration to the individual aggregates is realized. Selecting the correct equipment and formulation are two key steps.
Good dispersion is attributed to concurrent distribution and dispersive mixing (Figure 4).
Full dispersion in a polymer matrix requires time and energy.
For production efficiency there will be a time/energy and performance balance that will be particular to any given product.
Twin screw extruders, continuous mixers, and kneaders are commonly employed by the plastics industry for compounding carbon blacks.
Twin screw extruders may dominate the plastics compounding due to their well understood technology and scale-up, flexible design with barrel, screw and feeding configurations that serve a wide variety of resin chemistries and formulations. For highly loaded masterbatch and temperature-sensitive resin systems, Farrell Continuous Mixers (FCM) are efficient and can produce excellent quality masterbatch materials due to their counter-rotating non-intermeshing rotors, large free-volume chamber design, and internal temperature control. Kneaders, like those made by Buss, are based on simultaneous rotation and axial oscillation of the screw shaft, which offer a homogeneous shear field for mixing.
To achieve the desired compounding results, compounding process variables, namely, screw and barrel profiles, feeding configurations, residence time, temperature profiles and throughput need to be understood and perfected for each type of machine and compound system combination.
Formulation
There are four considerations here that should be shared.
- Masterbatch or Concentrate versus Direct Compounding – the masterbatch route is the dominant process compared to direct incorporation of carbon black to the final part pigment loading.
-
- Masterbatch processing
- The carrier resin is loaded with a high concentration (typically 15-50%) of carbon black in an energy-intensive mixing process such as a twin-screw extruder or continuous mixer.
- The masterbatch enables a higher level of dispersion with enhanced uniformity. This is particularly important for high surface area carbon black products.
- Masterbatch processing
- Polymer Type
-
- Differences in melt viscosity, chemical nature or compatibility with carbon black, and morphology of polymer will affect dispersion.
- Additives
-
- Dispersing additives developed to improve both pigment dispersion and processing conditions.
- Other additives include UV stabilizers, plasticizers, mold release, flame retardants etc. that can change dispersion of carbon black if compounded together. A masterbatch route for carbon black is often used for process efficiency and easy material handling.
- Other Considerations: Masterbatch Let Down Process
-
- Homogeneous letdown or dilution of a masterbatch into its final compound is essential for the best performance of carbon black product.
- Adequate compounding is needed when there is a large viscosity mismatch between masterbatch and letdown resin.
- The carrier resin of the masterbatch needs to be compatible with the letdown resin if not the same type.
- The presence of other fillers or domains in the compound may affect the distribution of carbon black and thus the performance.
Processing Challenges to Deliver High Jetness
-
- Tradeoffs between color performance and dispersibility (jetness is inversely correlated with dispersibility)
- Choice and control of compounding parameters that can significantly influence carbon black dispersion (agglomerates must be broken up to achieve adequate dispersion)
- Resin incompatibility or viscosity mismatch in the let-down process
Summary
In this blog, we have highlighted considerations that should be understood for extraction of the full color value from a high surface area carbon black for extreme jetness applications. Higher surface area carbon blacks are intrinsically much harder to disperse, less forgiving than products used in the medium to low color ranges, and proper process optimization (equipment and formulation) is essential. In a second blog we will cover in more detail the product design features and specific performance attributes for Birla Carbon products in this color space.
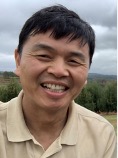
Dr. Jun Tian, PhD
Dr. Tian serves as Principal Scientist to lead a technology team and collaborate with our customers to develop carbon solutions to a variety of challenges for plastics applications. He joined Birla Carbon in 2013 and managed the plastics application laboratory to support the business growth. He holds a PhD degree in Chemical Engineering from the University of Connecticut.
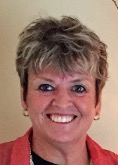
Dr. Natalie K. Harris
Dr. Natalie K. Harris began her career with Birla Carbon in 1990 at the European R&D Center in Bristol, UK, with responsibilities for the Materials Analysis Group. Dr. Harris relocated to the USA in 1998 with the role of Director, Applications Technology laboratory at the Corporate Headquarters in Marietta, Georgia, with the responsibility for managing programs for carbon black evaluations in tire, MRG, plastics, inks, and coatings. A few years later, Dr. Harris moved out of the laboratory environment to lead a global role in developing new products for the inks and coatings markets. Dr. Harris’s current role is Technical Business Development Manager, North America, for the plastics and MRG markets.
WANT TO LEARN MORE ABOUT CARBON BLACK AND THE PROPERTIES THAT MAKE IT IDEAL FOR YOUR PLASTICS, COATINGS, AND INKS APPLICATIONS?
Leave A Comment